原料药微粉一般指产品粒径小于20um的产品,微粉的气流粉碎是将粒径较大的颗粒或粉末粉碎成较小的颗粒或粉末的操作过程,一般要求粉碎后的产品粒径小于20um。其目的为减少粒径、增加比表面积、增加需求粒径的分布区间等。
药品粉碎的意义在于:1)粉碎后的药品有利于固体药物的溶解和吸收,可以提高难溶性药物的生物利用度;2)粉碎后的药品有利于混悬剂或固体制剂中各成分的混合均一性,混合度与各成分的粒径有关;3)粉碎后的药品有利于提高固体药物在液体、半固体、气体中的分散性,提高药品的利用率。
气流粉碎机主要分为对撞式与气旋式两种。其工作原理是利用压缩空气(或氮气)作为动力,将需粉碎的物料在粉碎机内加速至高速运动,使其与粉碎机内腔室进行碰撞而达到粉碎,主要是改变物料的粒径及其表面活性等。其可以将物料的粒径改变至1um~100um之间。下面,本人将结合自身工作经验,对药品微粉粉碎技术作一些初步探讨。
气旋式粉碎机在使用过程中影响微粉粉碎效果的因素主要有以下几个方面。
1)影响产品粒径的原因主要有粉碎物料进料速度及粉碎压力。粉碎压力是最主要的控制参数,同一物料在相同进料速度下,粉碎压力越大,单位产品受到的参量就越大,碰撞粉碎效果就更好。
2)较高的粉碎压力粉碎后的产品粒径较小,但是产品粉碎压力超过13bar后对产品粒径改变有限。如果粉碎压力达到13bar粉碎出来的物料仍未达到我们所需要的结果,建议寻找其他更合适的粉碎方法。
3)改变粉碎后产品粒径分布可以通过调节气流粉碎机的分布管及分级器来实现。在不改变的粉碎压力及进料速度的情况下,若要获得粒径越小的产品。
(1)可以将气流粉碎机的分布管调节至最低端,可以使物料在气流粉碎机内停留时间增加,停留时间的增加就等于增加了产品粉碎的碰撞时间,粉碎效果更佳。
(2)可以将气流粉碎机的分级器调节至最上端,分级器调节至最上端相当于减少了分级器内的空间,粉碎时作用在粉碎物料上面的气流能量损耗减少了,粉碎效果自然就好的。在实际生产中为了达到粉碎效果及产能的要求,一般将调节气流粉碎机的分布管及分级器结合起来使用,以达到最佳效果。
4)气流粉碎机的选型特别是粉碎机腔室形状对产品粒径的影响。圆盘式气流粉碎机腔体内结构一般有直角过渡与椭圆型过度两种,采用直角过渡的粉碎机在直角处物料是没有碰撞速度的,粉碎效果不理想。粉碎机腔体内采用椭圆形过渡的物料会随气流形成一个气旋,粉碎效果有明显的提高。但是椭圆型过渡机机器的制造工艺更加复杂决定了一次性投入成本更高,这需要企业根据自身需要来合理选型。
5)上下分级器。在粉碎机选型时候尽可能的选择带有上下分级器的设备。上下分级器可以防止大颗料物料进入上部分级器而随气流进入气固旋风分离器。因此选成带上下分级器的气流粉碎设备可以有效减少大颗粒物料对粒径的托尾现象,使产品粒径分布更加集中。
6)气流粉碎机加速喷嘴的角度。加速喷嘴的角度决定了物料在气流粉碎机腔体内停留的时间,也就决定了物料粉碎后的粒径。加速喷嘴越朝向粉碎机中心,产品停留的时间就越短,粒径就越大。在生产实践中证明加速喷嘴与气流粉碎机内环切线夹角在30°~40°时候是微粉产品粉碎效果最好的角度。
7)气流粉碎机加速喷嘴的直径。喷嘴的直径越大,单位时间内通过空气的量就越大,单位产品受到的能量就越大,产品粒度相对就越小。
8)气流粉碎机进料喷嘴的角度。进料喷嘴的角度决定了物料在粉碎机外腔室內的初速度,通过使用不同角度的进料喷嘴的可以调节物料在外腔室内的初速度,物料以相对较高的初速度通过加速喷嘴进入粉碎机的内腔内,从而能够得到粒径相对更小的产品。
9)气流粉碎机腔材质的选择:若物料粘性比较大而硬度不算是太高时可以选用PTFE材质的粉碎机腔体,PTFE材质的腔体可以有效避免大量物料粘连在粉碎机腔室内壁;硬度较大的物料采用不锈钢材质的内腔,不锈钢材质的内腔硬度较大基本可以满足绝大多数企业对粉碎的要求,其还有易清洁维护等优点,若是生产无菌产品,其可以支持在线纯蒸汽灭菌,现大多无菌制药企业使用的是316L材质的粉碎机内腔;对于硬度特别大的物料,不锈钢材质的内腔室无法满足生产需要的情况下可以选用陶瓷材质的腔体,陶瓷材质的腔体具有硬度大,耐磨损等优点,但其也有维护保养难,无法在线纯蒸汽灭菌等不足之处。
10)在物料的粉碎过程中经常碰到粉碎腔室内积料及起皮情况,其主要的原因有:
(1)物料粘性大,可想办法降低物料粘性(如通过降低物料水份含量来降低产品粘性)。
(2)腔体内物料太多,可以通过减少进料速度的方法来解决。
11)通过以上方法都无法达到理想粉碎效果的物料,可以考虑采用深冷粉碎方式来对物料进行粉碎。粉碎气体最好选用氮气,氮气有更好的稳定性及降温后没有冷凝水,若使用压缩空气,降温后冷凝水会结冰,冰渣随气体通过滤芯时会将滤芯击破。在实际运用中一般将气体通过冷干机进行降温冷却至-4℃以下,用冷却后的气体与物料相遇后物料温度会降低,粘度也会随之降低物料表面张力改变使物料变脆,更容易于达到粉碎至更小粒度的要求。因为物料在碰撞粉碎的过程中因高速运动会发热,物料温度会升高,故此方法特别适用于热敏性的物料粉碎工作。此方法缺点就是技术要求过高,设备投入较大,运行成本较高。
2 在粉碎过程中常出现的问题
1)粉碎机磨损太快。(1)物料硬度太大,此时应选用比较合适材质的粉碎机内腔。(2)设备长时间以较高粉碎压力运行,这种情况需要周期性的更换损耗件。
2)粉碎产品不均一。粉碎后的产品一般为单峰,若出现双峰或多峰主要原因有:
(1)粉碎压力不稳定。解决办法:在气源设备供气量能够满足工作所需气量的基础上,保证气源最低供气压力比工作压力高2~3bar。
(2)进料速度不稳定。解决办法:检查进料阀门处是否有堵塞;物料是不是粘性太大,流动性不均一,稳定的控制进料速度。
(3)粉碎机腔室内形成了滤饼。解决办法:暂停粉碎工作,清除粉碎机腔室内的滤饼后再恢复生产。
3)检测方法的影响。粉碎后的产品粒径检测结果达不到要求,在排除粉碎过程中会产生的问题后产品粒径检测结果仍达不到要求的结果可以考虑分析粒径的检测方法是否合理。例如物料粘性较大,粉碎后物料易结团,若采用干法检测方法显然是不合适的,此时可以考虑使用湿法进行检测,使物质在溶液内充分分散后再进行检测,这样得到的结果才是最真实的检测结果。
4)旋风分离对粉碎效果的影响。粉碎后的物料经旋风分离后旋风分离器内的压力大约保持在200~300mbar,这种压力下可以使用包装袋在旋风出料口对物料直接进行包装,这种情况是旋风分离最佳状态。若旋风分离器内压力过大,说明粉碎机出料口出气量较大,会对粉碎效果有影响。
3 结论
原料药微粉在现代制药应用中越来越广泛,市场对微粉产品的需求逐年增长。微粉的气流粉碎工艺具有对药品污染低、产量高等优点被企业广泛采用。流化床气流粉碎的特点有气源压力高、管道及设备受压大等特点,这些都是存在一定的安全隐患的风险点,在粉碎过程中如何使用尽可能低的气流压力生产出符合要求的微粉产品需要我们在实践中不断的去探索。
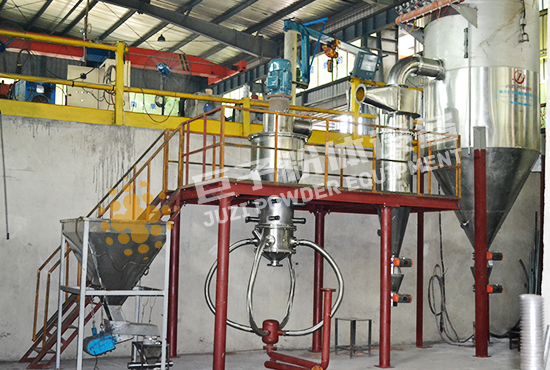